
FIRST-M Consulting Ltd.
Failure Investigation
Infrastructure Reliability & Safety
Science & Technology of Materials
From Science to Solutions: Corrosion and Metallurgical Consulting Services
ADVANCES IN SCIENCE
MAJOR TECHNICAL ADVANCES FROM THE WORK OF SHIPILOV AND COLLABORATORS
Summary: Research—mainly pioneering or exploratory when there were few or no earlier studies to refer to or rely upon to predict an outcome—spanned the areas such as (i) mechanistic understanding of stress corrosion cracking (SCC), corrosion fatigue crack growth (FCG), and hydrogen-induced cracking (HIC), (ii) developing advanced metallic materials with exceptional resistance to cracking under in-service conditions, and (iii) preventing in-service failures in complex engineering systems, including space, nuclear, and naval technologies. The investigations—which were conducted using novel experimental approaches and unique and overly sensitive equipment specially developed for each ongoing project—have challenged how the research community thinks about and understands materials behavior exposed to in-service settings and allowed the development of advanced structural materials to address modern and future challenges in materials science and engineering. The materials included high-strength low-alloy steels, stainless steels, carbon steels, and aluminum, magnesium, and titanium alloys.
Highlights: (1) The world’s first experimental method was devised for quantitatively defining the extent of HIC in corrosion FCG. The task has been most crucial in environment-induced cracking research since the 1950s; it was first addressed by Uhlig (1950), Hoar and Hines (1956), and Davis and Butler (1958). (2) Interdisciplinary research into underlying mechanisms of FCG and mechanical behavior of materials exposed to chemical environments allowed, for the first time, designing highly resistant to cracking materials for high-risk and safety-critical applications, including aluminum alloys, titanium alloys, and high-strength low-alloy steels. These novel crack-resistant materials have been (and still are) used in real-world applications and highly harsh environments, like space and the deep ocean. The genuinely world-class level of this work is supported by the fact that globally no other crack-resistant steel/alloy has been (purposely) designed in at least the last 40 years or so.
Most Important Contributions to the Field of Materials Science and Corrosion Science:
-
While at Oak Ridge National Laboratory, Shipilov pioneered research on a problem termed irradiation-assisted fatigue corrosion cracking (IAFCC), which is associated with the structural and functional integrity of the core components of aging water-cooled nuclear reactors, including naval (nuclear) reactors.
-
Note: If not addressed immediately, the problem may affect the availability of 30 nuclear-powered submarines and five Nimitz-class aircraft carriers (at an estimated cost of $104.85 billion) in service with the U.S. and Allied navies, including eight Ohio-class ballistic missile submarines (SSBNs), which operate beyond or well beyond their stated design limits.
-
In addition, according to the U.S. Department of Energy, the problem, along with irradiation-assisted stress corrosion cracking (IASCC), is “the highest interest in extended life scenarios” of 95 commercial reactors that generate nearly 20% of the electricity consumed in the United States.
-

The Ohio-class ballistic missile submarine USS Tennessee (SSBN 734), powered by an S8G nuclear reactor (220 MWt). Designed to operate for 30 years, she was commissioned in 1988 and is still in service 35 years later. Currently, nine ballistic missile submarines (SSBN) and four guided missile submarines (SSGNs) (each costing $3.18 billion in 2021 dollars) of 18 Ohio-class submarines and their 13 S8Gs operate beyond or well beyond stated design limits. (U.S. Navy photo by Mass Communication Specialist 1st Class James Kimber.)
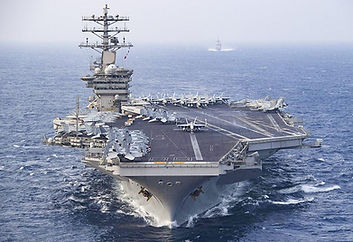
The aircraft carrier USS Nimitz (CVN 68), powered by two A4W nuclear reactors rated at 550 MWt each. Designed to operate for 40 years, she was commissioned in 1975 and is still in service 48 years later. The Nimitz and the USS Dwight D. Eisenhower (CNV 69) (each costing $10.1 billion), like their four A4Ws, operate well beyond their stated design limits. In addition, the USS Carl Vinson (CVN 70) and her two A4Ws achieved their design limits in 2022. (U.S. Navy photo by Mass Communication Specialist 3rd Class Elliot Schaudt.)
-
Developed a critical experiment for conducting the world’s first in-core investigation of IASCC under cyclic loading and electrochemical control to provide reliable experimental data, allowing for examining the validity of various hypotheses and determining the efficacy of something previously untried regarding IASCC; this experiment also is the first in identifying the mechanism for crack propagation under the influence of high-temperature water (up to 347 °C, 15.5 MPa) undergoing active radiolysis and intense radiation emitted directly from the core of an operating reactor.
-
Note: In the experiment, IASCC is treated as a multi-scale aging mechanism. It allows for the first time linking the cracking behavior of materials to their irradiation-affected mechanical properties and microstructural features (including microchemistry), fatigue processes, solution chemistry, oxide/metal-electrolyte interfaces, and the neutron flux.
-
For the investigations, Shipilov designed an experimental irradiation assembly and associated remote-sensing instrumentation, allowing in situ and operando monitoring of electrochemically controlled IASCC in cyclically loaded fracture-mechanics specimens in the U.S. Department of Energy’s (DoE) High Flux Isotope Reactor (HFIR), which provides one of the highest steady-state neutron fluxes of any research reactor in the world and has a pick thermal neutron flux density of 2.5E+15 n/cm^2·s, which is 50 to 100 times higher than cores of commercial nuclear power plants.
-
The estimated time needed to develop the first set of measures for preventing IASCC in existing water-cooled nuclear reactors worldwide, using the innovative experimental set-up—along with field data collected in the nuclear industry and lessons learned at other research laboratories (especially at the OECD Halden Reactor Project in Norway lasted from 1992 to 2018 and the Japan Materials Testing Reactor (JMTR) Project that started in 2003)—ranges from two to three years from completing the project’s first task in 2017. The timing depends solely on available funding—which cannot be an issue when dealing with the multi-billion-dollar technical problem that may put at risk the ability of nuclear power to play a crucial energy role in the future—and access to HFIR, which operates for only seven cycles a year, each cycle lasting about 24 days (less than six months per year).
-
The estimated time needed to develop, for the first time, an austenitic stainless steel and nickel alloy resistant to in-core IASCC ranges from three to four years from completing the project’s first task in 2017. The timing depends solely on available funding and access to HFIR.
-
-
First quantitatively defined the extent of hydrogen-induced cracking (HIC) in corrosion fatigue crack growth (FCG). The achievement was regarded in some quarters as “the most important breakthrough in corrosion science since the late 1970s requiring a ‘paradigm change’ in the theory of corrosion, particularly in environmental cracking.”
-
Note: New research findings did not support the information disseminated in textbooks and conference proceedings about corrosion fatigue, the most common cause of mechanical failures in a wide variety of industries.
-
The breakthrough made it possible to develop, for the first time, highly resistant to (hydrogen) cracking advanced structural materials.
-
It also made it possible for researchers to study, for the first time, the influence of environmental, metallurgical, and mechanical variables on the role of HIC in corrosion FCG—all first studied by Shipilov (with the goal to design novel cracking-resistant materials).
-
By controlling susceptibility to HIC—which depends on hydrogen accumulation that modifies the properties of materials, makes the materials brittle, and can result in a premature fracture if stressed beyond a certain threshold—engineers can reduce the likelihood of failure and extend the operating lifetime of complex engineering systems, including high-risk systems (e.g., high-pressure vessels and pipelines) and those operated in most extreme environments such as space, the deep ocean, and the nuclear reactor core.
-
In 2010, the breakthrough was recognized with the Technical Achievement Award of NACE International, a professional organization that serves nearly 38,000 members in over 140 countries and is recognized globally as the premier authority for corrosion control solutions.
-
-
Theorized, proved experimentally, and introduced into materials science and fracture-mechanics practice new threshold parameters—a crack tip stress intensity factor KHIC, stress intensity factor range ΔKHIC, and critical crack growth rate (da/dN)cr—that characterize the onset of corrosion FCG according to a HIC mechanism as in Figure 1.
-
Note: The KHIC parameter indicates the intensity of the stress field in the material ahead of the crack front at exceeding which a hydrogen-accelerated crack extension starts. In other words, KHIC is a parameter that characterizes a material’s resistance to HIC. Unlike other microstructurally sensitive mechanical properties, KHIC allows, for the first time, precisely to measure a material’s susceptibility to HIC; the parameter has been successfully used for developing novel materials resistant to HIC and hydrogen embrittlement.
-
Like KISCC, the new parameters KHIC, ΔKHIC, and (da/dN)cr are not the invariant properties of a material; the parameters depend on environmental factors, which influence the material’s susceptibility to HIC and corrosion FCG. Consequently, it is essential to ensure that appropriate values of KHIC, ΔKHIC, and (da/dN)cr are used in each (specific) case.
-
In most cases, KHIC determined at the complete/maximum coverage of the metal surface at the crack tip by hydrogen atoms (θH = 1) better (more precise) represents the susceptibility of the material in question to environmental cracking than KISCC. In specially selected electrolytes, KHIC might be less or much less than KISCC, and it can even be determined in materials (presumably) immune to SCC when KISCC is very high (close to KIc) or cannot be measured. All this makes the experimental approach based on KHIC more sensitive for determining and studying the susceptibility of materials to environmental cracking than that based on KISCC.
-
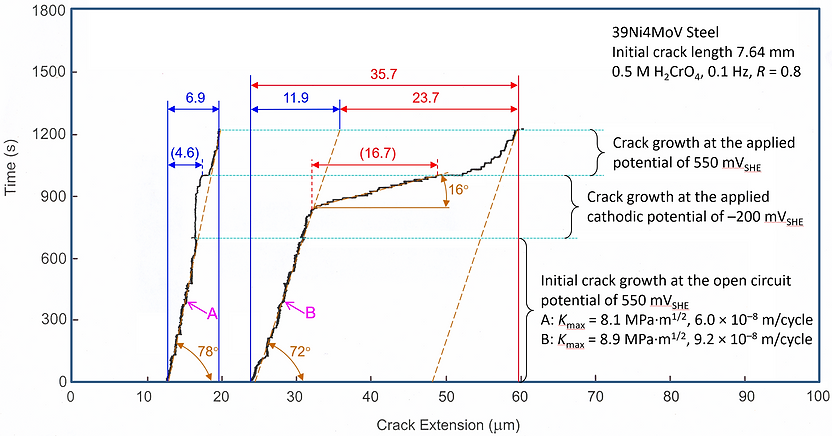
Figure 1. Diagram fragments indicating changes in corrosion FCG rates in high-strength low-alloy steel after cathodic potential application when Kmax was either (A) lower or (B) higher than the critical value of 8.3 MPa·m^1/2, which was designated as KHIC. Note: Accelerated crack growth did not start directly after the potential was applied but after a delay of about 100 s. The delay seemed to reflect the kinetics for processes (both at the steel/electrolyte interface and in steel) associated with an incubation period required for the necessary (critical) amount of hydrogen to concentrate ahead of the crack to provide conditions for HIC to occur. The accelerating effect of cathodic potential on crack growth when Kmax exceeded KHIC caused by HIC.
-
Proved experimentally (the first time this was done) that minor environmental changes produce substantial changes in the occurrence and intensity of fracture and fatigue in metals and that nominally similar environments produce different results. The findings reveal that: (i) the susceptibility of alloys to subcritical crack growth depends mainly on the specific chemistry and electrochemistry at the metal-electrolyte interface, as in Figure 2 (left), and to a lesser (though also significant) extent on the stress levels, strength, and metallurgical and chemical features of the alloys, as in Figure 2 (right), and (ii) materials with the same level of strength and/or with a similar chemical composition may have vastly different limits in terms of their chemical stability and susceptibility to subcritical crack growth.
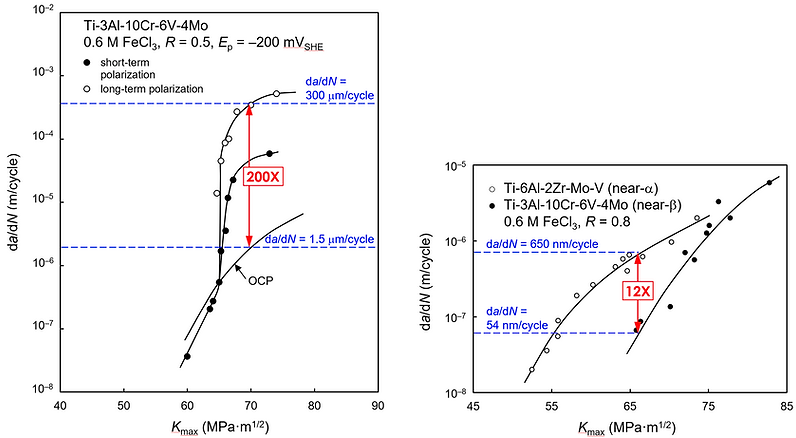
Figure 2. Corrosion FCG rates in titanium alloys at open circuit potentials (OCP), as well as under short- and long-term cathodic polarization. Note: The effect of an electrochemical potential on crack growth rates (left) was much more pronounced than the effect of strength and metallurgical and chemical features of the alloys (right).
Significant Contributions to the Field of Materials Science and Corrosion Science:
-
Devised a successful electrochemical crack-tip controlled experiment to conduct in-situ electrochemically controlled studies of and the effect of hydrogen charging on corrosion FCG in high-performance steels and alloys. This was the first time such studies were undertaken.
-
Developed an experiment that allowed for the first time to study the “true corrosion FCG” behavior of high-strength materials that are highly susceptible to stress-corrosion cracking (SCC). (Note: Before Shipilov’s groundbreaking studies, researchers could study either “stress corrosion FCG” in high-strength materials susceptible to SCC or “true corrosion FCG” in low-strength materials that were immune to SCC under constant load.) This experimental approach allowed us to demonstrate (the first time this has been done) that corrosion FCG rates in highly corrosive solutions could be lower or even much lower than crack growth rates in moderately corrosive solutions, including ambient air.
-
Innovated novel experimental methods (which drew on general theories about hydrogen behavior in titanium and its alloys) that first identified the accelerating effect of applied cathodic potential on the corrosion FCG of titanium alloys. (Note: Before the groundbreaking studies, it was believed that corrosion FCG in titanium alloys could be prevented by cathodic protection.)
-
Developed and first performed experiments identifying the accelerating effect of applied cathodic potential on SCC and corrosion FCG in aluminum and magnesium alloys due to HIC (with V.A. Marichev, 1986). (Note: In the literature, aluminum and magnesium alloys were (and still are) believed to be immune to hydrogen embrittlement and HIC. It was also believed that corrosion crack growth in the alloys could be prevented by cathodic protection. For example, according to Speidel (1975), “The stress corrosion crack growth rate in aluminum alloys can be dramatically (e.g., by a factor of more than one thousand) reduced by cathodic protection.” The latter is undoubtedly not always the case, as first shown by Marichev and Shipilov).
-
Note: In 1986, it was one of the earlier research, if not the earliest one, that used the fracture-mechanics approach to study corrosion fatigue crack propagation in magnesium alloys for biomedical applications, e.g., as novel biodegradable temporary implants.
-
The use by the engineering community of the knowledge about SCC of aluminum alloys—which was available before 1986—explains well why SCC has been responsible for 90% of all service failures of high-strength aluminum alloys (including 7079-T6, 7075-T6, and 2024-T3). Most failures could have been avoided during the last 30 years if the groundbreaking research of the mid-1980s had been implemented.
-
-
First evaluated the effect of corrosion inhibitors on FCG in steel exposed to an aqueous solution saturated with hydrogen sulfide (H2S) and showed that hydrogen sulfide corrosion inhibitors—in that study, dioctyl-aminopropionitrile (DOAPN), known as IFKhANGAZ-1—slowed corrosion FCG in steel with HRC 29 to approximately half when crack growth rates were less than 1.5 x 10^-7 m/cycle (15 nm/s). This crack growth rate probably corresponded to the formation rate of a stable and protective oxide film at the front of a slow-growing crack in the presence of the inhibitor. It was experimentally confirmed that the protective action of the inhibitor was caused by decreasing the role of HIC in corrosion FCG (Shipilov, 1986).
-
Note: This was one of earlier research, if not the earliest, that used the fracture-mechanics approach to study crack growth in H2S-containing solutions; it was the earliest crack-growth study in an H2S-containing solution under electrochemical control. This pioneering and groundbreaking study demonstrated the possibility of inhibiting the propagation of a subcritical (sharp) crack in materials exposed to H2S-containing solutions.
-
Conducting experiments in such a harsh chemical, extremely flammable, and highly toxic (very “extreme”) environment required him to design a special (Plexiglass) H2S corrosion chamber to avoid a leak of H2S but allow adding an inhibitor to the H2S-containing solution during a test. The experimental setup allowed applying cyclic loading (0.1 Hz at R = 0.5), monitoring crack growth in real-time (with the then world’s highest average crack extension resolution of about 1 µm), and applying a cathodic potential to a specimen inside the chamber.
-
Pioneering Contributions to Research:
In 1983, Shipilov initiated fundamental studies on corrosion FCG behavior and the role of HIC in corrosion FCG in advanced metallic alloys. This research integrated knowledge and experimental principles from metallurgy/materials science, chemistry, electrochemistry, and fracture mechanics. Consequently, in 1987, he earned the first Ph.D. degree in Russia for fracture-mechanics research on environment-induced cracking. As indicated in the list below, since his groundbreaking Ph.D. work, he has further developed and expanded theories, experimental tools, and cross-disciplinary approach that has resulted in innovations and research findings beneficial to and applicable across several industries.
-
Devised an experiment that first allowed comparing the increment of hydrogen-induced crack growth per cycle and critical distances ahead of a growing crack, including the distance to the location of maximum tensile stress ahead of the crack, the sizes of cyclic and monotonic plastic zones, and the depths of hydrogen penetration due to lattice diffusion and dislocation sweeping. It was first demonstrated, in 1999, that the position of the hydrogen-induced corrosion FCG process zone does not always correlate with a plastic-zone size; in addition, there is no correlation between the increment of crack growth and the location of maximum tensile stress ahead of the crack as in Figure 3.
-
Note: Up to Shipilov’s groundbreaking research, the position of the "fracture process zone" was still being discussed and had no direct experimental confirmation. Some results from this comparative study challenged well-known and conventional (beginning in the late 1950s) theoretical views on hydrogen-induced crack growth mechanisms. In addition, no existing theory of hydrogen embrittlement can explain the direct (experimental) observation showing that a critical crack growth rate (da/dN)cr can increase by two orders of magnitude if a stress ratio (R = minimum load/maximum load) decreases from 0.9 to 0.1, but a hydrogen-accelerated corrosion FCG rate (da/dN)p only slightly depends on R between 0.1 and 0.9 (Figure 4).
-
As a preliminary observation, the study, for the first time, questioned the existence of plastically deformed zones ahead of (slowly) growing corrosion fatigue crack at Kmax < KIc and stress-corrosion crack at K < KIc (Shipilov, 1999). (Note: In 2016, researchers at ORNL, based on the Electron Backscatter Diffraction (EBSD) data, concluded that “most plastic strain, if it appeared during crack propagation, was localized in the 5–10 µm [surface] layer. The strain tended to be localized to some grains, whereas other grains near the crack edge remained undeformed.” In 2019, EBSD images collected by researchers at Argonne National Laboratory confirmed the absence of a plastically deformed zone ahead of an SCC crack in Alloy 152; however, the study’s most important finding was not addressed by ANL researchers—so much faith exists in the presence of the plastically deformed zone that it is easier to believe that it is there even if it is not seen on EBSD images. The absence of a plastically deformed area ahead of subcritical cracks was also confirmed by EBSD images obtained by researchers from Japan, Korea, and Finland who studied cracking in austenitic stainless steels between 2020 and 2023; the researchers did not mention or prefer not to discuss these crucial findings.)
-

Figure 3. Comparison between hydrogen-enhanced corrosion FCG rates and critical distances ahead of a growing crack in a titanium alloy (left) and magnesium alloy (right) at open circuit potentials and under cathodic polarization. Note: Contrary to theories developed between the late 1960s and the early 1990s and still used today, there is no correlation between crack growth rates and “critical distances ahead of the growing crack” imposed by these theories.
-
First demonstrated that (i) ΔKHIC increases with decreasing R and, what was more, a linear relationship exists between ΔKHIC and R: (ii) susceptibility of materials to HIC under cyclic loading, characterized by the KHIC parameter, can be either equal to or lower than under constant load; (iii) the HIC susceptibility does not depend on R if the metal surface at the crack tip is completely (or almost completely) covered by hydrogen atoms—such a complete coverage (θH = 1) is achieved when further decreasing a potential does not further reduce KHIC; (iv) in the case of θH < 1, a higher KHIC is required for HIC, especially under cyclic loading; (v) the accelerating effect of cathodic polarization on crack growth rates is more pronounced at higher R, meaning that the relative contribution of HIC to environment-induced crack growth (in comparison, e.g., with stress-assisted dissolution) increases with increasing R and is maximal under constant load.
-
First demonstrated, as in Figure 4, a numerical relationship between the critical crack growth rate corresponding to the onset of corrosion FCG according to a HIC mechanism (da/dN)cr and the stress intensity factor range (ΔK). The finding led to and confirmed a new conclusion that FCG is controlled by the level of ΔK (or stress range) rather than the level of applied Kmax (or maximum stress). (Note: Up to when Shipilov made the finding in 1999, this question was still being discussed and had no direct experimental confirmation.)
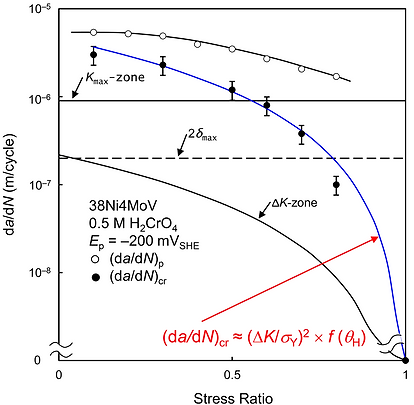
Figure 4. Effect of stress ratio on the hydrogen-enhanced corrosion FCG rate (da/dN)p, the critical corrosion FCG rate (da/dN)cr, and the size of the monotonic plastic zone (Kmax-zone) and cyclic plastic zone (ΔK-zone) ahead of the crack. Note: There is an apparent correlation between (da/dN)cr and ΔK (primarily, at R < 0.8), confirming that corrosion FCG in high-strength low-alloy steel was controlled by ΔK.
-
First proved experimentally that the morphology of the fracture surface (e.g., intergranular versus transgranular) depends on a crack growth rate and does not represent, and should not be linked to, a specific crack growth mechanism, as previously thought.
-
Note: The conclusion contradicts the opinion that has been prevalent in the literature for decades with no piece of factual evidence. The breakthrough was made after Shipilov designed a sensitive experimental set-up with the highest (at that time) crack increment resolution, less than the smallest grain size. It allowed studying crack growth in real-time and knowing what is happening with a crack and its growth every single second rather than waiting for an hour or more (e.g., days, weeks, or months) until the crack would advance a millimeter or so, i.e., grew through dozens of grains before an average crack growth rate could be estimated (rather than measured like in Shipilov’s tests). The research explained that the morphological distinction between intergranular SCC (IGSCC) in alkaline soils observed in the U.S. and called “high-pH SCC” (or “classical SCC”) and transgranular SCC (TGSCC) in neutral-pH soils observed in Canada and called “near-neutral-pH SCC” (or “non-classical SCC”) is misleading; in fact, this is the same type of failure (neither “classical” nor “non-classical”), but hydrogen-accelerated crack growth in pipeline steels depends on the conductivity of soil, dependent on its physical properties and the chemical composition.
-
-
Proved experimentally that there is no correlation between the metallurgical variables such as grain size (e.g., the prior austenite grain size) and the cyclic (“reversed”) plastic zone at ΔK values corresponding to a maximum percentage of intergranular fracture during (corrosion) FCG in ferritic and pearlitic steels, as has been thought since the early 1970s.
Other Significant Contributions to Materials Science, Corrosion Science and Engineering, and Solid Mechanics:
-
Reviewed historical aspects and experimental trends in environment-induced cracking studies of metals for more than 140 years since 1873, when the first recorded research on record was conducted. This study is the first to gather and analyze information that serves as a touchstone for future research in the field.