
FIRST-M Consulting Ltd.
Failure Investigation
Infrastructure Reliability & Safety
Science & Technology of Materials
From Science to Solutions: Corrosion and Metallurgical Consulting Services
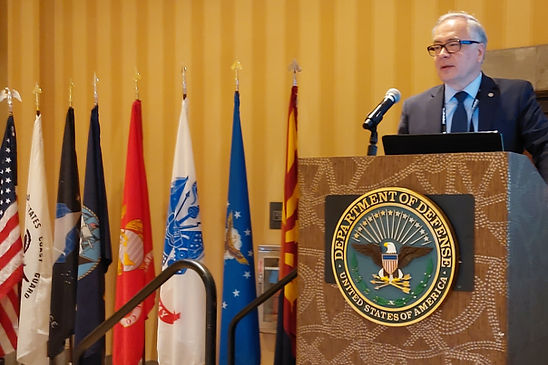
Shipilov at the 2023 DoD Corrosion Prevention Technology and Innovation Symposium in Tucson, AZ, August 15, 2023.
The first-ever fact-based assessment of the impact of materials deterioration and corrosion on the readiness of U.S. naval aviation was presented at the 2023 DoD Corrosion Prevention Technology and Innovation Symposium in Tucson, Arizona, August 14–17, 2023.
The 2023 U.S. Department of Defense (DoD) Corrosion Prevention Technology and Innovation Symposium had a purpose “to facilitate information exchange between the U.S. Government participating organizations, private industry, academia, and the Allies with a focus on reducing the impacts of corrosion on costs, availability and safety of systems and facilities used by the Armed Forces.” With an estimated cost of corrosion of military equipment and infrastructure of approximately $20 billion every year, corrosion—without a real attempt to address it for over 20 years—remains the number one cost driver in the U.S. Armed Forces’ life-cycle costs. The lack of success in addressing corrosion in the U.S. Armed Forces, with a focus on the Navy, was demonstrated based on documented facts in Shipilov’s paper titled “Impact of Materials Deterioration and Corrosion on the U.S. Naval Aviation’s Readiness” at this Symposium.
The paper was based on the report titled “Impact of Corrosion on the United States Navy’s Overall Readiness” that he prepared for the National Commission on Military Aviation Safety—which was created by Congress in the John S. McCain National Defense Authorization Act (NDAA) for FY2019 “to examine past mishaps and make recommendations to the President, Congress, and the Defense Department for improving aviation safety and readiness in the military”—in February 2020. The subsequent audit in September 2021 by the DoD Office of Inspector General, which was requested by the U.S. House Armed Services Committee, confirmed that “corrosion may contribute to [decreasing] mission capability rates” and recommended: “that the Commander, Naval Air Forces, assess the actions implemented to address corrosion and determine whether these actions resulted in fewer instances of corrosion, reduced costs, or improved readiness.” In 2023, Shipilov updated his nine-page report from 2020 and expanded it to a 46-page paper, which became the first-ever fact-based study on this subject. It is not seen from his updated paper that the Navy has implemented the DoD Office of Inspector General’s recommendations. Really, why should something be suddenly changing over two years if no changes have been made in the previous 20 years? Also, it is puzzling what could be the reason behind the resistance to changing the status quo.
Abstract of Shipilov’s paper: “The U.S. Navy faces high corrosion costs, surpassing the expenses of most-price ships and weapons systems. Naval aircraft operating in harsh environments are especially susceptible to corrosion, which affects nearly all their components and materials. Corrosion is responsible for over a quarter of the maintenance expenses for naval aviation—every hour of maintenance related to corrosion results in multiple hours of lost availability. Lengthy delays in aircraft maintenance jeopardize the Navy and Marine Corps’ ability to maintain readiness. Corrosion and especially stress corrosion cracking/corrosion fatigue is one of the main (technical) causes why Admiral W.F. Moran, Vice Chief of Naval Operations, told the U.S. House Armed Services Committee that ‘the Navy’s overall readiness has reached its lowest level in many years’ and is declining. The lack of attention to these issues in the U.S. Armed Forces became especially evident when a Marine Corps KC-130T Hercules crashed in 2017 in Mississippi, killing all 16 servicemen on board. The investigation revealed that the growth of a corrosion fatigue crack was ‘ultimately the root cause of this catastrophic mishap.’ This crash and dozens of other aircraft accidents could have been prevented if the DoD had made a rule to seek the advice of subject matter experts rather than just talking about corrosion costs and battling cosmetic corrosion relying on the expertise of and mainly, if not exclusively, dealing with barely trained graduates of short corrosion courses. Misunderstanding what corrosion (theoretically and practically) means and how it should be addressed is the leading (and only) cause of the lack of visible success in ‘fighting corrosion’ across all military services, especially in naval aviation.”
Here is a quote from the Introduction to the paper: “The two following sections of the paper, ‘Availability and Mission-Capable Rates: Strike Fighters’ and ‘Aging and Corrosion Maintenance Costs of Strike Fighters,’ bring attention to more critical (and still corrosion-related) topics, such as military readiness—defined as ‘the military’s capacity to engage in combat and fulfill assigned missions and task’ [20]. The sections make the paper substantially different from all previous discussions, including those by the DoD [1–7,9], typically focused on the cost of corrosion, the basics of corrosion, and diagrams with squares, circles, triangles, and arrows in between. The hope that ‘squares, circles, and triangles with arrows’ drawn on slides could help to ‘win the war on corrosion’ has been and still is traditional at the DoD since at least 2003 [21].”
SUMMARY AND CONCLUSIONS
-
“Corrosion costs the DoN [Department of the Navy] nearly $10 billion per year, more than its most expensive ships and weapons systems. For example, the [nuclear-powered aircraft carrier] USS Gerald R. Ford (CVN 78)—the most expensive ship ever built in the U.S. Navy and worldwide—cost on average about $1.2 billion annually to build [between 2009 and 2012]. It is three times less than what the DoN spends each year dealing with aircraft corrosion alone.
-
In the 20 years—after the DoD established the Corrosion Policy and Oversight Office in 2003—corrosion has cost the DoD at least $400 billion. If corrosion was controlled, the DoD could realistically save enough funds to build one Ford-class aircraft carrier (costing about $12.8 billion per unit) every two years. The total cost of all ten world’s most advanced aircraft carriers of the Ford class, ordered by the Navy, is estimated to be around $130 billion, less than the DoD could (potentially) save in the past 20 years.
-
According to the DoD, the F/A-18E/F Super Hornet fighters—the Navy’s ‘mainstay’ of carrier aviation operations—have the highest total corrosion cost among the DoN’s aviation assets. Based on the FY2017 data, corrosion of naval aviation was estimated in 2021 to cost $3.76 billion per year, over 27% of the DoN’s total maintenance expenditure. From FY2017 through 2020, the DoN spent more than $2 billion only to address corrosion-related problems for its F/A-18 aircraft, with almost $1.2 billion (56%) attributed to the newest F/A-18E/F Super Hornets. Moreover, it was recently revealed that the F/A-18E/F fleet ages faster than the preceding fleet of F/A-18C/D Hornets.
-
Corrosion, like (or even more than) decades ago, affects the Navy’s overall readiness. In no fiscal year between 2011 and 2021, the F/A-18E/F and F-35B fleets met the annual MC [mission capable] goal. The F-35C fleet met its goal only in two years out of nine. The Navy’s F/A-18E/Fs had higher MC rates in 2015 than in 2021, typically near 40%. The actual MC rate for F-35Cs in FY2021 was 19% below the fighter’s minimum performance target and 51% below the fighter’s objective performance target. Moreover, the radar-absorbing coating on the F-35C planes, the Navy’s first stealth fighters, degrades unexpectedly quickly on aircraft carrier decks.
-
Besides costing the DoD billions of dollars annually and being the dominant cause of the Navy’s reduced readiness, corrosion poses numerous safety risks. The concern is particularly acute when associated with the safety of naval aircraft and crews. The lack of knowledge and sufficient expertise within the DoD and its research organizations/contractors in materials properties, corrosion theory, and especially environmental cracking—which has been responsible, as shown in this paper, for many structural failures and accidents, including fatal aircraft crashes—hinders the Navy and Marine Corps’ ability to respond rapidly to national security and foreign commitments. This should not be the case because today’s fundamental science and technology can practically and reasonably control materials deterioration and cracking in most cases.
-
A new approach is necessary to change the status quo and effectively combat corrosion to reduce related costs and decrease the impact of corrosion on the readiness of the Navy and Marine Corps aircraft while increasing their safety. Instead of discussing year after year minor issues—and relying on the knowledge of the graduates of short (typically five-day) corrosion courses hoping they are qualified enough to prevent the corrosion of military equipment, including the world’s most advanced multi-role fighters—it is time to shift the focus and start addressing real-world existing and most critical problems caused by corrosion. This can only be achieved if the expertise and experience of renowned corrosion and materials scientists are used. After 20 years of effort—without any specific plan for what to do and achieve year by year—and spending hundreds of millions of dollars on numerous (R&D and educational) programs with little to no outcomes, the DoD (through its Corrosion Policy and Oversight Office) should seek real help to develop and implement science-based corrosion prevention and control strategies. Failing to do so will result in further mounting expenses (beyond the $400 billion lost since 2003), as seen in the past few decades.”
For more information, see S.A. Shipilov, “Impact of Materials Deterioration and Corrosion on the U.S. Naval Aviation’s Readiness,” Proceedings of the 2023 DoD Corrosion Prevention Technology and Innovation Symposium, paper no. DOD- AUG22-19858 (Washington, DC: Department of Defense, 2023).