
FIRST-M Consulting Ltd.
Failure Investigation
Infrastructure Reliability & Safety
Science & Technology of Materials
From Science to Solutions: Corrosion and Metallurgical Consulting Services
CLIENT INQUIRIES
MATERIALS PERFORMANCE AND CORROSION PROTECTION
We have been studying corrosion and materials performance since the early 1980s, including advanced scientific topics at national laboratories and research universities, providing consultations on aspects from simple domestic problems (e.g., an oil spill from a domestic fuel oil tank) to complex space, nuclear, and deep-ocean problems.
Our experience and expertise help clients find resolutions to engineering materials’ corrosion and degradation problems. These problems involve design, materials, environments, and operations. We can help to develop an approach to resolution and mitigation.
We strongly believe the following:
-
With aging high-risk technologies (e.g., in nuclear and petroleum sectors) and the nation’s core infrastructure, it is not sufficient to wait and “learn” from accidents and disasters,
-
Most failures and industrial accidents that have taken place in the past were preventable and could have been stopped if (world-renowned) experts on corrosion, materials performance, failure analyses, and infrastructure reliability had been called in,
-
Through advanced technology, it is possible to evolve an extensive range of experimental and monitoring equipment, which can be applied to solve nearly every conceivable problem and even predict corrosion failures that have not yet been observed but could occur after long times, such as those associated with water-cooled nuclear reactors.
For example, in many cases, the proactive evaluation approach for maintaining engineering structure availability (PEAMESA) allows us to answer typical client inquiries, such as the following:
-
Why did this material and structural component fail?
-
What is the most reliable and fastest way to fix the problem?
-
How long should the original material and component have lasted?
-
How long will the fixed material/component last, and under what conditions?
-
How should we operate to prevent further failures?
This approach includes the following seven steps:
-
Component study: Determine the component design and material features. For example, determine the presence of notches and types of base and weld materials.
-
Stress and load study: Determine applied and residual stresses in the components. This includes the determination of stresses from all potential loads. The applicable load combinations must also be determined.
-
Environment study: Determine the environment in contact with the component surface(s). The physicochemical properties of the environment must also be determined.
-
Degradation study: Given the components and environment studies results, determine the component’s susceptibility to various degradation mechanisms. In addition, this study can also resolve the location and orientation of potential failure (e.g., cracking). The results can prioritize the components and provide recommendations to mitigate, repair, replace, inspect, monitor, and evaluate the failure.
-
Consequences of degradation study: Determine the consequences of degradation in the components if failure were to occur and go undetected. The consequences should consider the impact on plant safety, plant availability and financial implications.
-
Allowable flaw size evaluation study: Given material features, flaw orientation and geometry, stress, and environment, the proper flaw size evaluation can be performed. This evaluation would require some assumptions about crack configuration (e.g., assume it is not a wall-through
crack). These conservative assumptions may be refined if the flaw is not dispositioned under the initial allowable flaw size criteria. The new study could consider the remaining wall ligament and spacing of multiple cracks. -
Pre-outage planning study: Pre-outage planning studies should focus on the following items:
-
Conclusions of proactive studies discussed above (steps 1-6),
-
Identification of regulatory requirements regarding components,
-
Understanding the various options for dispositioning/mitigating a failure (e.g., cracking).
With a comprehensive understanding of these three items, a short and long-term program may be outlined which can identify the following:
-
Which components should be inspected over the next 5 to 10 years? (This includes the inspection needs at each outage and an expanded inspection scope if a failure is observed,)
-
What mitigation actions are necessary to reduce the potential for failure?
-
What repair/replacement activities should be implemented?
The PEAMESA might look simple, but in fact, it requires an engineer or a failure analyst to attend multidisciplinary training, which no university or college currently provides. For example, how do interested individuals train to become corrosion engineers? This cannot be done by obtaining a degree in the subject because no such specialization is available at the undergraduate level in most countries, including Canada. Many people involved in corrosion control either have no degree or have studied in fields with a remote connection to corrosion at best. Most of these people became corrosion engineers/experts through on-the-job experience or by individual study.
Moreover, it is not widely known or accepted that the problem of materials failure has several sources, the most significant of which is how engineers select which material to use in which industry. According to textbooks and undergraduate courses on the mechanical behaviour of materials, engineering students learn how to choose materials solely by assessing their mechanical properties, with little or no consideration of how those mechanical properties will interface with the specific operating parameters found within different industries. (Note: This approach was established in the nineteenth century when most modern industrial sectors did not exist.) It is why practical engineers, including young graduates, are usually unprepared to prevent the failure of materials under in-service conditions, including fatigue, fracture, and corrosion: they simply do not have the relevant background and knowledge.
The benefits provided by PEAMESA could be better understood if we remember that structural corrosion and mechanical failures represent any change in the size, shape, and/or materials properties of a structure that renders it incapable of satisfactorily performing its intended function.
As first proposed by Starkey, a systematic classification allowing for the prediction and description of a failure mode is based on defining three categories: (1) manifestation of failure, (2) failure-induced agents, and (3) location of the failure.
Each specific failure mode (Table 1), which can occur in engineering practice, can be identified as a combination of one or more manifestations of failure together with one or more failure-induced agents and the location of the failure. The four manifestations of failure are as follows: (1) elastic deformation; (2) plastic deformation; (3) rupture or fracture; and (4) material change: metallurgical, chemical, or nuclear. The four failure-induced agents include the following: (1) stress: steady, dynamic, transient, cyclic, or random; (2) reactive environment: chemical and nuclear; (3) temperature: low, room, elevated, steady, transient, cyclic or random; and (4) time: concise (very short), short, or long. The two failure locations are (1) body type and (2) surface type.
Some of the 80 failure modes commonly observed in practice are listed in Table 1. FIRST-M Consulting Ltd. is familiar with most of the failure modes.
TABLE 1. The Commonly Observed Modes of Materials Degradation and Failure
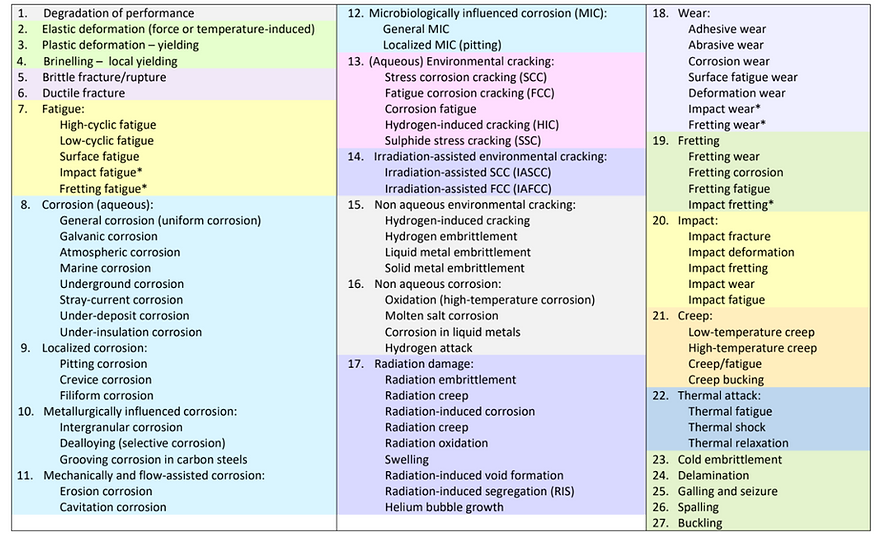